-
Micro Stepper Motor
-
Permanent Magnet Stepper Motor
-
Geared Stepper Motor
-
Linear Stepper Motor
-
Slider Stepper Motor
-
Hybrid Stepper Motor
-
Small DC Gear Motor
-
ROV Thruster Motors
-
Micro Metal Gearmotor
-
Micro Gearbox
-
Position Control Stepper Motor
-
3D Printer Stepper Motor
-
Stepper Motor Driver
-
DC Motor Controller
-
Lead Screw And Nut
-
Andres BlancoThe thruster have arrived correctly. I tested them on the ROV and we are very happy with the result. The epoxy interior finish is very good and the power of the motors in relation to the size is quite good.
-
Gregoire LangeThe cooperation between Changzhou Vic-Tech Motor Tech and our company was just great. Good understanding of our needs, great willing to solve our problems. I recommend !
-
David MoleveltProfessional and clear communication. Order was shipped in time. Counter connectors where added to the shipment. Driver works like we agreed !
-
Buildstorm Private LimitedThe product works as expected, it was packed nicely. Seller responds very quickly and helps in making a buying decision. They are ready to customize the product for you.
-
Ashley GriffinShipment was received very quickly. Product was well protected by packaging. Company rep was cordial and kind. A Plus rating!
3V 12VDC Micro Stepper Motor Driver Controller With Manual Buttons
Place of Origin | Jiangsu, China (Mainland) |
---|---|
Brand Name | VIC-TECH |
Certification | RoHS |
Model Number | PM4_207 |
Minimum Order Quantity | 1 Unit |
Price | $16~22.8/unit |
Packaging Details | Standard export package, or can be customized |
Delivery Time | 15 work days after confirming the payment |
Payment Terms | T/T, Western Union, MoneyGram, |
Supply Ability | 10000 Units per month |
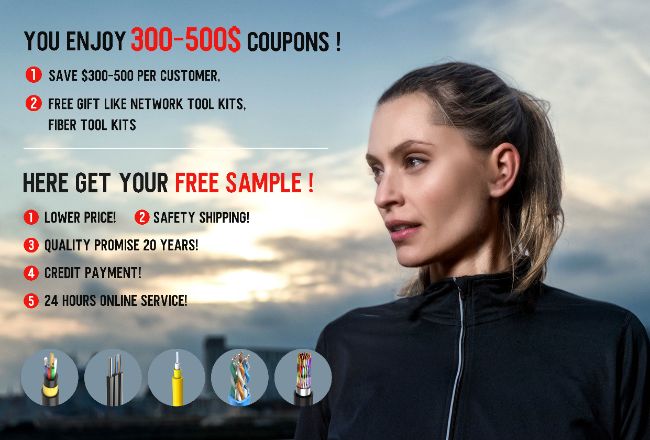
Contact me for free samples and coupons.
Whatsapp:0086 18588475571
Wechat: 0086 18588475571
Skype: sales10@aixton.com
If you have any concern, we provide 24-hour online help.
xMotor Type | Stepper Motor | Voltage | 3~12V DC |
---|---|---|---|
Highlight | 12VDC Stepper Motor Driver Controller,3VDC Stepper Motor Driver Controller,12VDC Stepper Motor Driver Board |
PM4_207 micro stepper motor driver controller with manual buttons
This is our 207 stepper motor driver, it’s used to control 2 phase stepper motors with manual buttons. The operating voltage is from 3V to 12V DC, depends on rated voltage of the motor you use.
There is a 2.0mm connector where you can connect the motor with this driver.
A. MOTOR (A+ /A- /B+ /B-):
Motor access port:
A+ /A- Connect to motor phase A,
B+ /B- Connect to motor phase B.
Also there are 6 ports where you connect with power supplier, and DIR, CP, EN signal from signal generators
- Power and control signal input port:
(input signal level ≤DC 5V)
1. VCC power input terminal DC: 3-12V, (Please select the actual input voltage according to the needs of the motor.)
- GND Power negative terminal
- 3.3V drive control board output
- CP DIR EN input signals are: pulse, direction, enable, the above input signals are common ground
EN = 1 (floating), the motor enters the automatic offline state, the motor will go offline after stopping for 5 seconds, and the motor winding will lose power.
EN = 0 (grounded), the motor enters the forced enable state. When the motor is running/stationary, the motor windings are always energized.
- BY: spare port
- The input signals are common cathode connection (ie common ground input)
You can connect this motor with on VCC and GND port, this way, you can control this motor with button combination,
The other way to use this motor is connect this driver with signal generator, so it can receive signal from other controllers.
Keyboard description:
(Q: start key, T: stop key, A: click forward key, D: click back key,
ON: key press, OFF:Key release)
No. |
Button combination
|
Description |
1 | A = ON | When the motor is at a standstill, press the click key, and the motor will start to run forward manually; |
2 | A+Q= ON | When the motor is at a standstill, press the A + Q key, and the motor will start to manually accelerate forward; |
3 | A+T = ON | When the motor is at a standstill, press the A+T button, and the motor starts to decelerate manually in forward direction; |
4 | D = ON | When the motor is at a standstill, press D button and the motor will start to run in reverse direction manually; |
5 | D+Q= ON | When the motor is at a standstill, press the click D + Q key, and the motor will start acceleration manually reverse direction ; |
6 | D+T = ON | When the motor is at a standstill, press the click D + T key, and the motor will start to decelerate manually reverse direction; |
7 | Q = ON | When the motor is at a standstill, press Q button, and the motor will start to run automatically; |
8 | A = ON | When the motor is running automatically, press A key and the motor will start to accelerate; |
9 | D = ON | When the motor is running automatically, press D button and the motor will start to decelerate; |
10 | Q+A= ON | When the motor is running automatically, press the Q + A key, and the motor will start to run automatically; |
11 | Q+D= ON | When the motor is running automatically, press the Q + D back button, and the motor starts to run automatically in reverse; |
12 | T+A (or T+D) = ON | When the motor is at a standstill, press the T + A (or T + D) key, and the motor starts to manually set the distance of automatic cycle running; |
13 | T+Q= ON | When the motor is at a standstill, press the T + Q button, and the motor will automatically reciprocate according to the manually set distance; |
14 | A = ON | When the motor is running in a reciprocating cycle, press A key to accelerate the motor reciprocating cycle; |
15 | D = ON | When the motor is running in a reciprocating cycle, press D button, and the motor will decelerate in a reciprocating cycle; |
16 | Q+A= ON | When the motor is running in a reciprocating cycle, press Q + A key, and the motor will reciprocate in a forward direction; |
17 | Q+D= ON | When the motor is running in a reciprocating cycle, press the Q + D key, and the motor will reciprocate in reverse; |
18 | T = ON | When the motor is running, press T button to stop the motor. |
Remark
|
Combination keys, press in the order given, the function can be executed |
Product display
(1) What is a stepper motor and a stepper drive?
Stepper motor is a special motor specially designed for precise control of speed and position. Its rotation is operated step by step at a fixed angle (called "step angle"), so it is called stepper motor. Its characteristic is that there is no accumulated error, every pulse signal sent from the controller is received, and the motor runs at a fixed angle under the drive of the driver, so it is widely used in various open-loop control.
The stepping driver is a power amplifier that can operate the stepping motor. It can convert the pulse signal sent by the controller into the power signal of the stepping motor. The speed of the motor is proportional to the pulse frequency, so the control pulse frequency can be precisely adjusted. Speed, the number of control pulses can be accurately positioned.
(2) What is the breakdown of the drive?
The stepper motor is determined by its own unique structure, and the “inherent step angle of the motor” (such as 1.2°/0.6°) is indicated at the factory. However, in many precision control and occasions, the angle of the whole step is too large, affecting the control precision, and the
vibration is too large. Therefore, it is required to complete the inherent step angle of a motor in many steps. This is called a subdivision drive and can realize this function. The electronic device is called a subdivision driver.
(3) What are the advantages of subdivision drivers?
Because the step angle that has passed each step is reduced, the step uniformity is improved, so the control accuracy can be improved.
The vibration of the motor can be greatly reduced. The low-frequency oscillation is an inherent characteristic of the stepper motor. Subdivision is the best way to eliminate it.
It can effectively reduce torque ripple and increase output torque.
These advantages are generally recognized by users and bring them benefits, so it is recommended that you use subdivision drivers.
(4) Why does my motor only work in one direction?
- The possible direction signal is too weak, or the wiring polarity is wrong, or the signal voltage is too high to burn out the direction current limiting resistor.
-
The pulse mode does not match, the signal is pulse/direction, the driver must be set to this mode; if the signal is CW/CCW (double pulse mode), the driver must also be in this mode, otherwise the motor will only run in one direction.