-
Micro Stepper Motor
-
Permanent Magnet Stepper Motor
-
Geared Stepper Motor
-
Linear Stepper Motor
-
Slider Stepper Motor
-
Hybrid Stepper Motor
-
Small DC Gear Motor
-
ROV Thruster Motors
-
Micro Metal Gearmotor
-
Micro Gearbox
-
Position Control Stepper Motor
-
3D Printer Stepper Motor
-
Stepper Motor Driver
-
DC Motor Controller
-
Lead Screw And Nut
-
Andres BlancoThe thruster have arrived correctly. I tested them on the ROV and we are very happy with the result. The epoxy interior finish is very good and the power of the motors in relation to the size is quite good.
-
Gregoire LangeThe cooperation between Changzhou Vic-Tech Motor Tech and our company was just great. Good understanding of our needs, great willing to solve our problems. I recommend !
-
David MoleveltProfessional and clear communication. Order was shipped in time. Counter connectors where added to the shipment. Driver works like we agreed !
-
Buildstorm Private LimitedThe product works as expected, it was packed nicely. Seller responds very quickly and helps in making a buying decision. They are ready to customize the product for you.
-
Ashley GriffinShipment was received very quickly. Product was well protected by packaging. Company rep was cordial and kind. A Plus rating!
12V Stepper Motor Controller / Permanent Magnet Dc Motor Controller SWT-203M
Place of Origin | Jiangsu, China (Mainland) |
---|---|
Brand Name | VIC-TECH |
Certification | RoHS |
Model Number | SWT-203M |
Minimum Order Quantity | 1 Unit |
Price | $20~30/unit |
Packaging Details | Standard export package, or can be customized |
Delivery Time | 15 work days after confirming the payment |
Payment Terms | T/T, Western Union, MoneyGram, |
Supply Ability | 10000 Units per month |
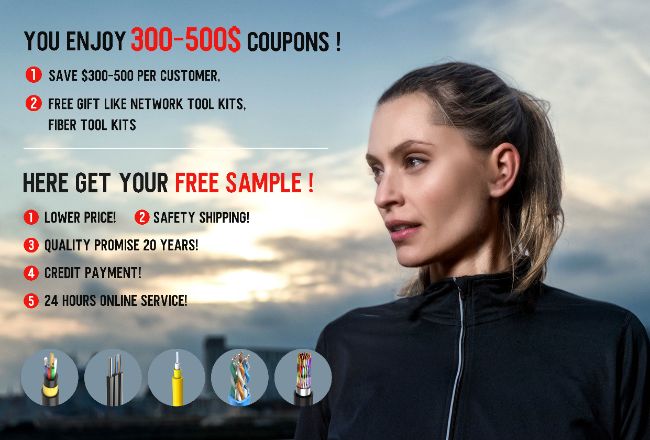
Contact me for free samples and coupons.
Whatsapp:0086 18588475571
Wechat: 0086 18588475571
Skype: sales10@aixton.com
If you have any concern, we provide 24-hour online help.
xMotor Type | Stepper Motor | Voltage | 12V |
---|---|---|---|
Weight | 250g | ||
Highlight | bipolar stepper motor driver,micro stepper motor driver |
SWT-203M micro stepper motor driver for permanent magnet stepper motor and hybrid motor
SWT-203MS Stepper Motor Driver Instruction Manual
1. This driver is suitable for driving two-phase hybrid stepping motor with phase current ≤3.2A.
2. Adopting techniques and processes such as constant current chopping and noise absorption suppression to make stepper motor system
High reliability, small size, light weight, high efficiency, balanced operation, static and high
Features such as high speed torque.
Mechanical Dimension:MM
Second, the wiring instructions
1.CP+(CW+) is connected to external controller +5V output
2.CP-(CW-) is connected to the external controller pulse signal output (forward direction pulse output)
3.DIR+(CCW+) is connected to external controller +5V output
4.DIR-(CCW-) is connected to the external controller direction signal output (reverse direction pulse output)
5.FREE+ is connected to external controller +5V output
6.FREE- is connected to the external controller reset output (motor is de-energized, low potential is valid)
7.A connected to stepper motor A phase
8./A connected to stepper motor A phase
9.B connected to stepper motor B phase
10./B connected to stepper motor B phase
11. GND is connected to the negative pole of DC voltage
12.DC ≤40V connected to DC voltage positive electrode
Third, the shape and installation size
note:
1. See the panel for other parameters of the drive.
2. The external controller is a single pulse signal
It is a step signal CP (pulse signal) and a direction signal DIR (level signal), and the external controller is a double pulse signal which is a motor forward rotation signal CW (pulse signal) and an inverted signal CCW (pulse signal)
number)
3. When the user is using, the dial switch 6 must be turned to the OFF position (SW6=1)
Product Detail Presentation
Wiring Instructuins
ON=0 OFF=1 | |||
Current SW7-SW10 | |||
7 8 9 10 | Current | 7 8 9 10 | Current |
0000 | 0.4A | 1000 | 2.0A |
0001 | 0.6A | 1001 | 2.2A |
0010 | 0.8A | 1010 | 2.4A |
0011 | 1.0A | 1011 | 2.6A |
0100 | 1.2A | 1100 | 2.7A |
0101 | 1.4A | 1101 | 2.9A |
0110 | 1.6A | 1110 | 3.0A |
0111 | 1.8A | 1111 | 3.2A |
Driver FAQ User Answers (Q&A)
(1) What is a stepper motor and a stepper drive?
Stepper motor is a special motor specially designed for precise control of speed and position. Its rotation is operated step by step at a fixed angle (called "step angle"), so it is called stepper motor. Its characteristic is that there is no accumulated error, every pulse signal sent from the controller is received, and the motor runs at a fixed angle under the drive of the driver, so it is widely used in various open-loop control.
The stepping driver is a power amplifier that can operate the stepping motor. It can convert the pulse signal sent by the controller into the power signal of the stepping motor. The speed of the motor is proportional to the pulse frequency, so the control pulse frequency can be precisely adjusted. Speed, the number of control pulses can be accurately positioned.
(2) What is the breakdown of the drive?
The stepper motor is determined by its own unique structure, and the “inherent step angle of the motor” (such as 1.2°/0.6°) is indicated at the factory. However, in many precision control and occasions, the angle of the whole step is too large, affecting the control precision, and the
vibration is too large. Therefore, it is required to complete the inherent step angle of a motor in many steps. This is called a subdivision drive and can realize this function. The electronic device is called a subdivision driver.
(3) What are the advantages of subdivision drivers?
Because the step angle that has passed each step is reduced, the step uniformity is improved, so the control accuracy can be improved.
The vibration of the motor can be greatly reduced. The low-frequency oscillation is an inherent characteristic of the stepper motor. Subdivision is the best way to eliminate it.
It can effectively reduce torque ripple and increase output torque.
These advantages are generally recognized by users and bring them benefits, so it is recommended that you use subdivision drivers.
(4) Why does my motor only work in one direction?
- The possible direction signal is too weak, or the wiring polarity is wrong, or the signal voltage is too high to burn out the direction current limiting resistor.
-
The pulse mode does not match, the signal is pulse/direction, the driver must be set to this mode; if the signal is CW/CCW (double pulse mode), the driver must also be in this mode, otherwise the motor will only run in one direction.